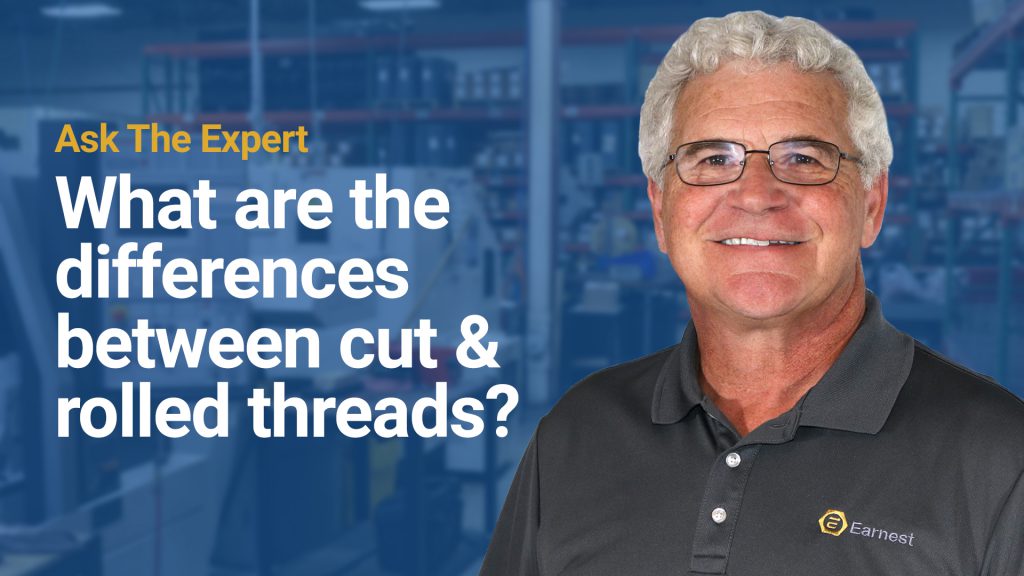
What are the differences between cut and rolled threads?
Are the threads cut or rolled? We are often asked this question in regards to how the threads were manufactured on a particular size bolt or screw that we stock. The main reason we are asked this question is because “rolled” threads are perceived to be superior to “cut” threads on externally threaded fasteners.
When a thread is rolled, it means the thread was formed by cold forming the steel by pressing the part between either two flat plates or round dies that have the thread pitch machined onto their face. As the part “rolls” through the dies, the pressure applied by the plates creates the thread without cutting or removing material.
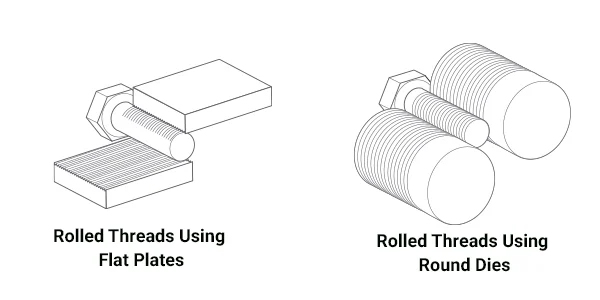
A cut thread (also called a machined thread) is made by machining away the material in order to create the thread form. Cut threads, as the name implies, are made by cutting away material.
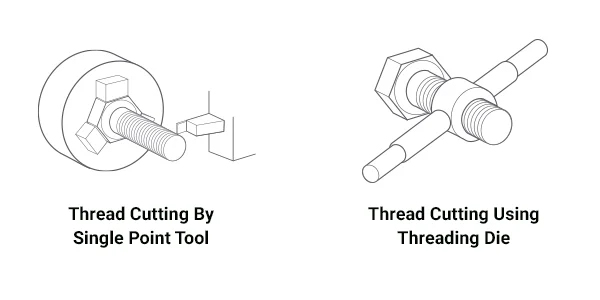
Customers who ask this question are typically looking for a product that they can offer their customer that has the highest perceived quality.
The reason rolled threads are perceived to be better than a cut thread is:
• Thread rolling dies create a thread form that has a rounded root radius.
• The rolling operation forces the steel’s “grains” to flow with the thread form.
• The cold working, of the thread rolling operation, increases the strength of the steel in the threads.
When you are dealing with non-heat-treated bolts (grade 2, grade A, low carbon steel, etc.) a rolled threaded part will have a higher strength than a bolt with cut threads in the area where the threads were formed. When a part is heat-treated (like grade 5 and grade 8 bolts) a cut thread and a rolled thread part will have the same strength. The hardness to which the part is heat-treated determines the strength and not how the threads were manufactured.
The form at the bottom (root) of the thread plays an important role in the “fatigue” resistance of the thread. A radiused (rounded) thread root does improve the thread’s fatigue resistance. Cut threads are often perceived to create a sharp point at the thread root. A sharp point at the root does make a thread more susceptible to fatigue failures as compared to a thread with a round root. Threads can be cut using a cutting tool that has a radiused point to create a rounded root thread. A heat-treated bolt with a cut thread that has a rounded root radius will have a comparable fatigue strength as compared to a heat-treated bolt with a rolled thread.
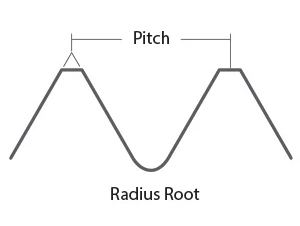
The fact is that a cut thread can be manufactured with a radius root that is equivalent to the radius root formed by a rolled thread. So for grade 5 and grade 8 strength level products, a cut thread can have the same fatigue resistance as a rolled thread.
Rolling the thread is a cost-effective way to make threads in high-volume operations. A cut thread is the most cost-effective way to make a thread for low-volume applications.
Earnest standard product is made with threads that are rolled prior to heat treatment. When we make a special, we will cut the threads. When we cut threads, we use cutting tools that will create a rounded root thread form that will provide fatigue resistance equivalent to a rolled thread product.
The best thread form (called the aircraft quality thread) is to roll the threads after heat treatment with a large root radius, called a UNJ thread form. A grade 5 or 8 strength level bolt that has had its threads rolled after heat treatment will provide the highest resistance to fatigue failures. If the parts have been heat-treated after the thread forming operation, the way the threads were manufactured (cut or rolled) does not provide a significant increase in the fatigue resistance.